
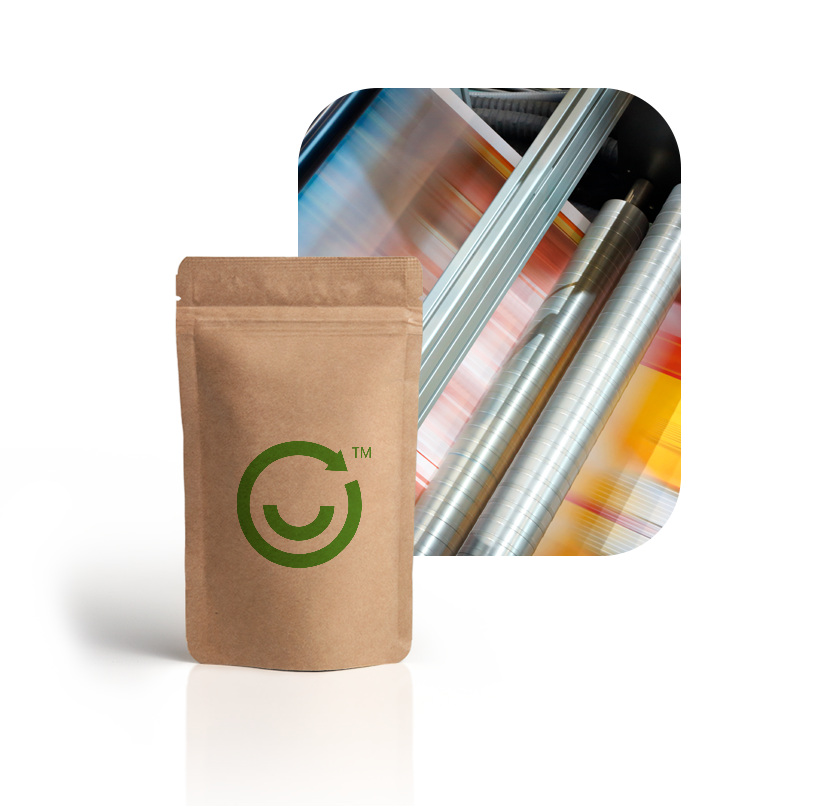

recyclable food packaging
The Enviraflex brand encompasses a range of eco-friendly films designed to make food and other types of packaging more sustainable. Central to this ethos is our flagship Enviraflex technology, which fuses a printed PE layer to a second, high-tech PE substrate without the use of adhesives to produce a 100% recyclable film that is compatible with existing thermal welding equipment.
Recyclable pouch films
100% polyethylene structures
Anti-fog, recyclable visor film
Biodegradable films
Recyclable laminates





How it works
Our core Enviraflex film is made using the Cellcoat T30 machine to fuse two substrates, creating 100% recyclable or compostable structures. The first is a pre-stretched, printable PE film called MDO. The unique properties of this material give it a higher melting point than other films – so once laminated with a food-grade PE liner, it can be used with standard thermal welding machines to produce flexible pouch packaging from a single, recyclable material.
Enviraflex films offer a uniquely environmentally friendly solution to the challenge of non-permeable packaging. Our technology can be used to produce sustainable, 100% recyclable pouches and laminated boxboard substrates, suitable for a wide range of applications including food packaging, arts & crafts, cosmetics and more.
Food packaging is one of the biggest generators of plastic waste. Manufacturers and buyers face ambitious environmental targets and increasing demand from consumers to reduce their carbon footprint. Enviraflex delivers practicality, hygiene and freshness for food packaging, in a planet-friendly format.
As well as being fully recyclable, Enviraflex requires significantly less energy in production than conventional wet lamination processes – further reducing its carbon footprint, and enabling manufacturers to do their bit for the environment at a lower cost.
Conventional printed laminates are usually made in a time consuming ‘wet lamination’ process that involves the use of adhesives which must then be dried before the product can be used. Made using our proprietary technology, Enviraflex is produced on the T30 thermal laminator in a glueless process that heats, cools and rolls the product in a single process. The result is a printed & laminated film that’s ready to use the same day.
Enviraflex has been designed as a two-part substrate to offer manufacturers complete convenience and flexibility in producing bespoke packaging in-house. The base substrate is compatible with digital print technology from HP, Canon, Ricoh, Xeikon and Screen as well as traditional litho, flexo and inkjet printing (including UV), and specialist technologies such as gravure and nanographic. As a result, it couldn’t be simpler to integrate Enviraflex and the T30 machine into existing production lines.
For more information on how to order Enviraflex
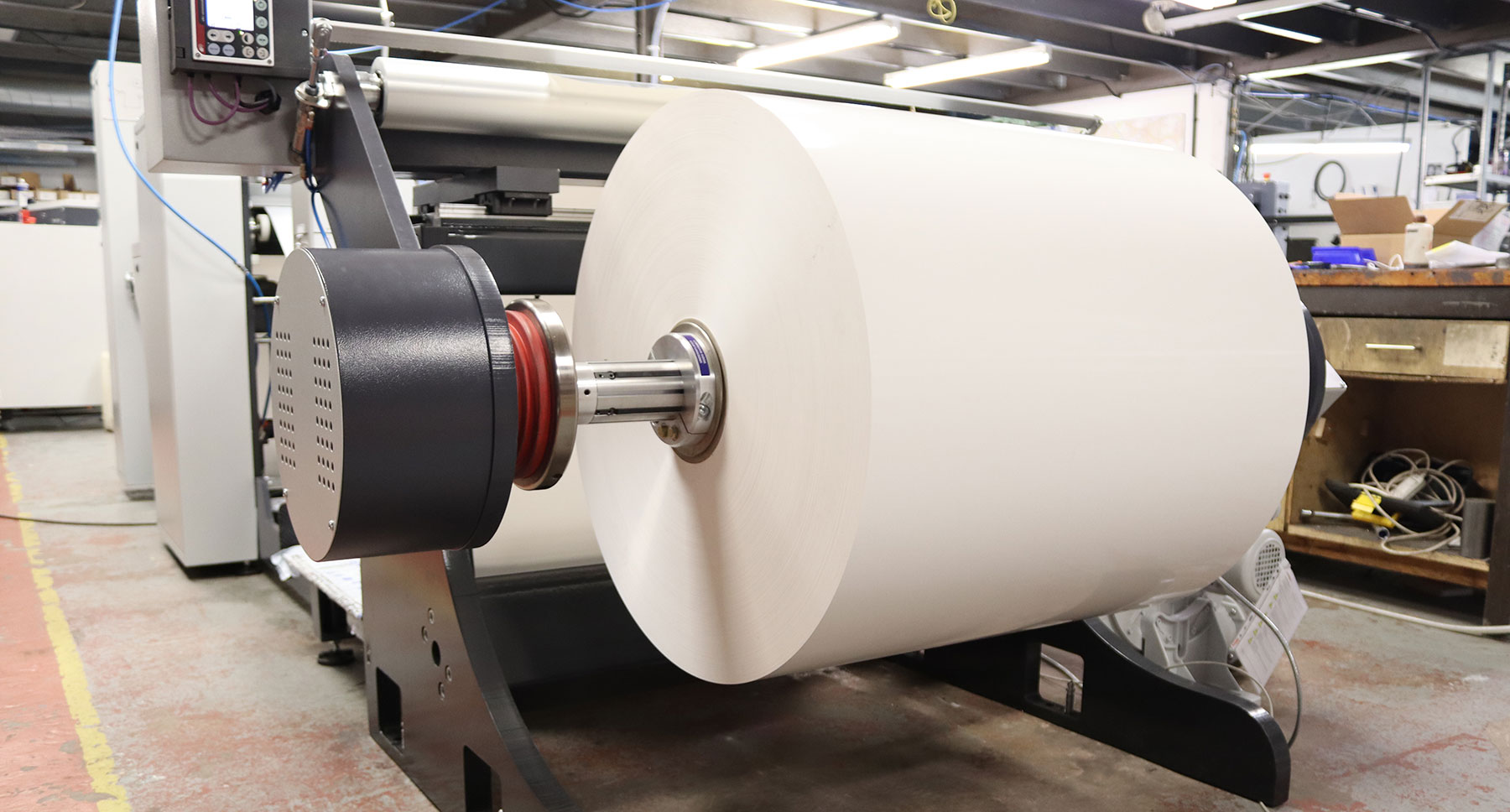
Reel to reel convenience
Conventional printed laminates are usually made in a complex ‘wet lamination’ process that involves the use of adhesives which must then be dried before the product can be rolled up ready for use. Made using our proprietary technology, Enviraflex is produced on the T30 thermal laminator in a glueless process that heats, cools and rolls the product in a single step. The result is a printed & laminated film that’s ready to use the same day.
Supreme printability
Enviraflex has been designed as a two-part substrate to offer manufacturers complete convenience and flexibility in producing bespoke packaging in-house. The base substrate is compatible with all existing print technology from HP, Canon, Ricoh, Xeikon, Screen and more. As a result, it couldn’t be simpler to integrate Enviraflex and the T30 machine into existing production lines.

We developed Enviraflex because we believe all food packaging should be 100% recyclable and we set about developing an innovative product that solved a range of food packaging production problems to help make our planet a better place.
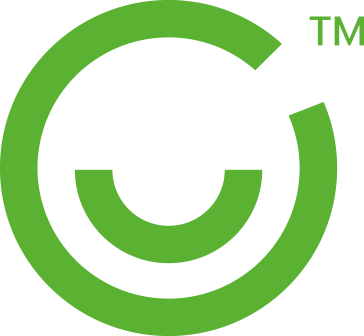